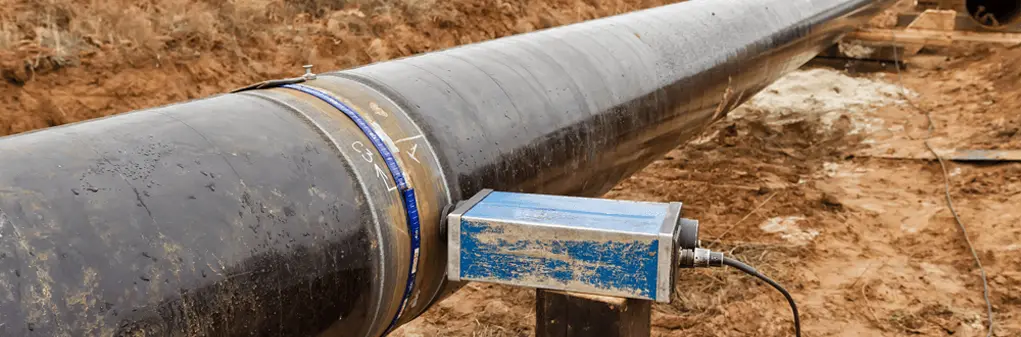
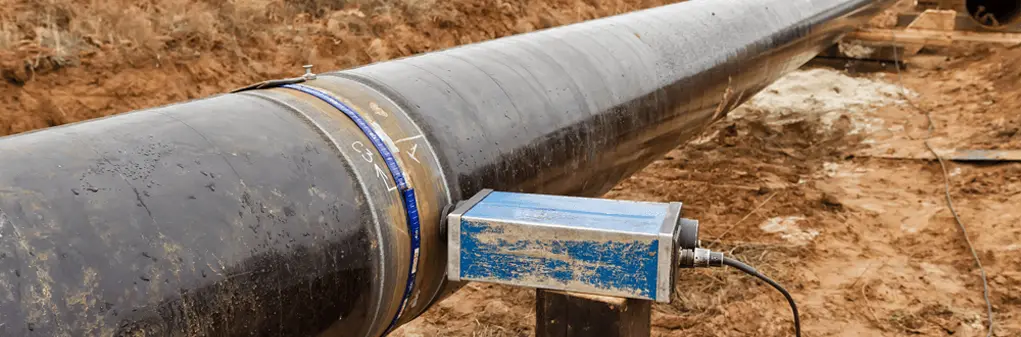

Want to share this article?
Pipeline Integrity Plus Risk Management Can Equal Zero Incidents
This is the second blog in our series on Pipeline Integrity Management. To read the first post, click here.
Above all, the most important factor for any pipeline project is safety.
In fact, every engineering company these days is sure to tout its safety record and claim to foster a “safe culture” that promotes stop work and other safety practices. But why? Undoubtedly, it is the steep cost that is incurred when pipeline failure happens. Pipeline failures can lead to devastating consequences, such as the loss of human life and wildlife, environment contamination, property damage, and finances. Ethical operators understand that these invaluable costs can never be adequately recouped nor recompensed. Therefore, ensuring the long-term integrity of pipelines remains top priority for pipeline operations, and it begins at the design and construction phases and continues into the maintenance stage.
Pipeline safety is possible with a consistent and thorough pipeline integrity management plan. Integrity management plans (IMPs) are crucial — and nowadays required — in order to successfully assess potential degradation, damage and the risks they pose to pipelines. Assessing these risks involves factoring in the likelihood and the consequence of failure. Pipeline risks are calculated by combining the likelihood of a hazardous event with its consequences (i.e., risk = a function of [probability consequence]). The likelihood of failure is linked to an asset’s condition; the consequence comprises the social, economic, health and safety, and environmental effects of pipeline failure and is associated with asset criticality. Ensuring the long-term integrity of pipelines remains top priority for pipeline operations, and it begins at the design and construction phases and continues into the maintenance stage. Poor evaluation of risks is often cited as the main reason for ineffective integrity management programs, leaving pipelines vulnerable to defects and sometimes failure. For example, a major pipeline ruptured in 2010 and lost nearly 3 million liters of heavy oil, which spilled into a stream near the Michigan’s Kalamazoo River. The operator’s safety management system proved to be deficient because it did not factor in the safety of integrity management or other operational processes. In other cases, pipeline operators lack sufficient data to successfully implement probabilistic risk models.
Operators need quality data from a reliable database to aid with identifying hazards during risk management activities. The best risk management process clearly defines what measures need to be in place in order to control and mitigate risks and maintain the pipeline safety and mechanical integrity. This includes performing risk assessments and analyses. While risk assessments can be used to identify potential hazards and their effects, risk analysis should not be the primary means to assess the overall integrity and safety of a pipeline. It is best to use both methods together. This is especially true for pipelines that were built and in operation prior to formalized regulations. Standard operating procedures greatly reduce the opportunity for pipeline failure as evident in the last decade. These company-developed procedures for pipeline design and construction should be congruent with corporate safety policies, experience, philosophy, business practices, industry best practices (e.g., API 1160 and ASME B31.8S), and federal standards. For example, the U.S. Department of Transportation Office of Pipeline Safety (US DOT OPS) regulations include design codes that outline the appropriate safety factors and quality control issues to implement during pipeline construction. To help strengthen pipeline safety practices, the industry continues updating and creating guidelines. In July 2015, the American Petroleum Institute announced that it would issue Recommended Practice 1173 “Recommended Practice for Pipeline Safety Management Systems Requirements” to address pipeline safety issues that current standards do not. The new Recommended Practice is a voluntary standard that focuses on creating a safety culture for pipelines, and it is based on the “plan-do-check-act” (PDCA) model with processes for tracking and reporting a company’s risk-mitigation activities.
Pipeline risk management starts with a company’s corporate management and should be thought of as a partnership with government agencies and local entities. Having a good, capable staff and management is also an important aspect risk management. Written procedures and processes are beneficial, but equally so is providing adequate training for operation and maintenance (O&M) personnel to ensure pipeline integrity and safe operations. If companies want a commitment to a “zero incident, zero accidents” safety culture, a solid pipeline integrity and risk management strategy is the key to doing so. In return, operators can expect regulatory compliance, cost savings in repairs and replacement (by mitigating failures), risk assessment and reliability, asset performance management, as well as improved integrity and profitability.
Want more information on how pipeline integrity can improve the safety and reliability of pipelines? Read our upcoming blog post, “Integrity Management Paves the Way for Effective Pipeline Design,” where we illustrate how effective pipeline integrity can aid with designing new pipelines.
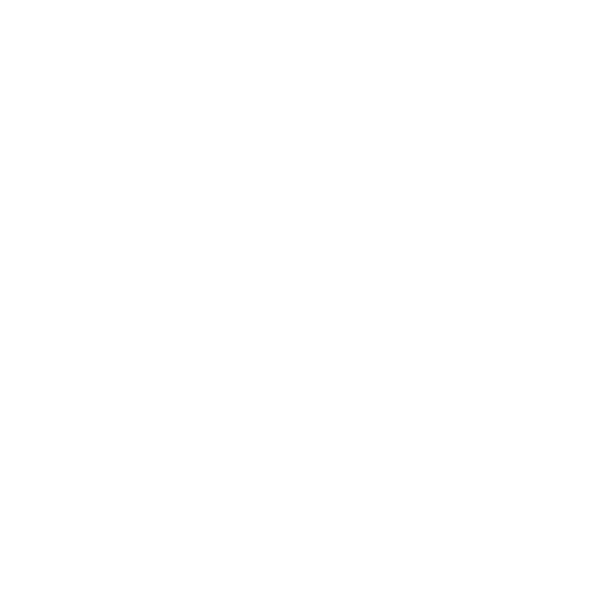