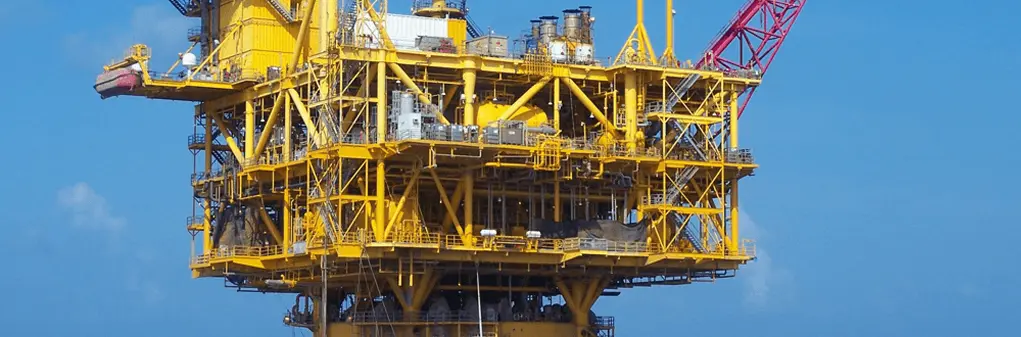
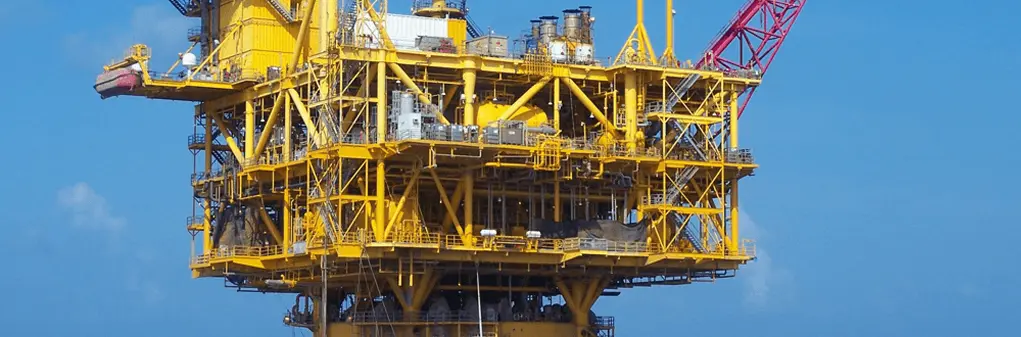

Want to share this article?
Reducing Weight of Offshore Facilities with Compact Well Testing Units
Reducing weight and conserving space on deepwater platforms and production facilities has always been a key area of focus for offshore producers.
This is understandable given that increased weight often results in higher costs and added complexity with regards to fabrication, installation, commissioning, and transport. In recent years, through advances in measurement equipment and remote-monitoring technology, well testing has become an area where operators have been able to achieve substantial savings – and they’re doing so by replacing conventional testing apparatuses with more compact and highly automated solutions.
Well testing is a necessary part of any production operation. In offshore operations, as many as 25 wells can be routed to a single platform. With conventional testing solutions, the product coming from each of these wells is tested by re-routing flow into a test separator. This allows operators to view various characteristics of each individuals well’s raw stream, including production rate, pressure, volume, temperature, and presence of impurities. The testing process itself plays a key role in maximizing production from offshore fields.
Although there are a number of different well testing solutions available on the marketplace today, most require a substantial footprint (~15ft x 25ft). Their weight is also significant, with some weighing in excess of 30,000 lbs. Complex piping manifolds are typically an ancillary component of conventional well-testing systems and can take up additional weight and space as well.
Replacing conventional well testing apparatuses with more compact and remotely monitored testing units can conserve both weight and space. Doing so also provides significant advantages during commissioning and installation. Integral to these units are multi-phase flow meters, which eliminate the need for bulky test separators. Multi-port flow selectors are also an important feature of compact well testing apparatuses and can minimize the requirement for large piping manifolds. Furthermore, because they can be remotely operated, producers gain real-time insight into the performance of each of their wells. The need to transport personnel to and from the platform to perform maintenance work and monitor the system is also greatly reduced, which offers benefits with regards to safety.
Compact well testing units are often associated with a higher up-front CAPEX; however, the benefits they offer in terms of OPEX over the life-cycle of a facility has made them an increasingly attractive option in the offshore environment.
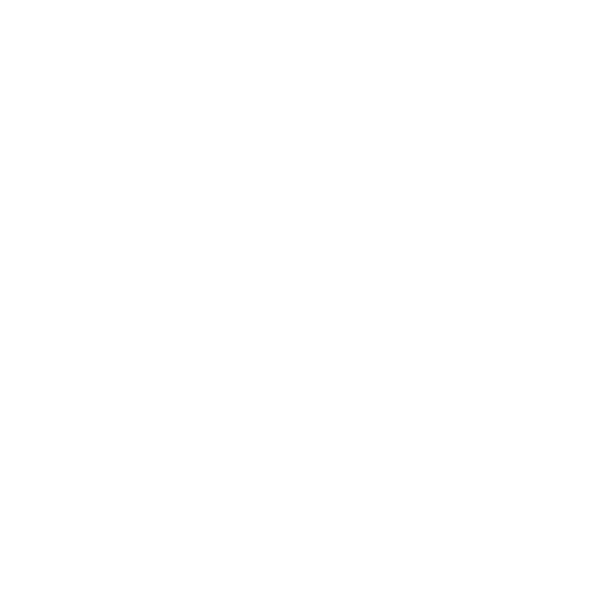