


Want to share this article?
Improving Offshore Drilling Safety through Risk Indicators and Mitigation
Risk mitigation in offshore oil and gas isn’t just about offering safety training and installing safety devices.
It’s a long-term process that involves research not only at the company level but also across the entire industry. In fact, a wide variety of risk-mitigation-based regulations and practices are codified around the world (PDF), including BAST (best available and safest technologies) and SEMP (Safety and Environmental Management Program). Yet there’s always more work to do to improve our understanding of offshore safety indicators and how they can be applied to better reduce risk in drilling and other activities.
Blowout prevention is a major component of risk mitigation in the offshore realm. As such, significant research has been made in attempts to analyze and improve upon existing safety indicators of an impending oil or gas blowout. Skogdalen et al., for example, published such research in 2011, suggesting numerous indicators related to schedule or cost, well incidents, operator well response, overall operation, and safety-critical elements. The proper use of these indicators means hastily made, unsafe decisions can be limited; well incidents can be reduced; issue response time can be decreased; training programs can be improved; and safety-related systems can be better maintained. “Safety indicators contribute to preventing systemic accidents,” noted the group, adding that they “should be developed for all drilling phases.”
Analysis of statistics related to offshore drilling safety also lends insight into how to better improve risk mitigation. In a series of two articles for Oil & Gas Journal in 2014, Mannan et al. compiled and analyzed such statistics from a wide variety of sources, looking for leading causes of injuries and deaths in the offshore sector. The group found “struck by” risks related to lifting, rigging, and drilling to be increasingly prominent and recommended that risk mitigation projects “should focus on operating procedures and risk assessments, particularly for these hazardous activities.” They also recommended that mitigation strategies better work towards “maintaining safety equipment, monitoring for indicators such as kicks or cement failures, and responding quickly when conditions are right for a blowout.”
Of course, once a risk mitigation program is implemented, it must be evaluated, updated, and maintained. Optimally, risk should be routinely monitored as part of program review, and any new risks or changes to existing risks should be evaluated in order to reassess the program. However, economic volatility has driven some companies to cut costs, in some cases negatively affecting risk mitigation strategies. Despite tough times, offshore operators must be cautious in their approach to cost cutting to ensure the highest levels of safety in the industry. “[S]afety is just as important now as it was when things were busy,” noted the Association for Energy Service Companies’ executive director Kenny Jordan in a report for Bloomberg.
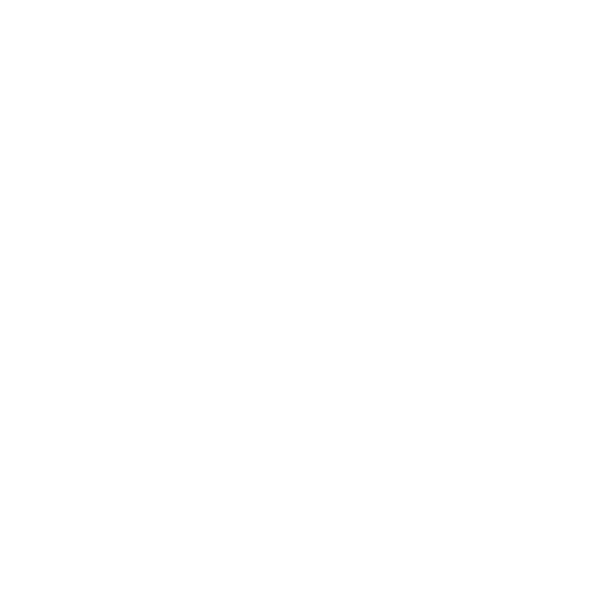