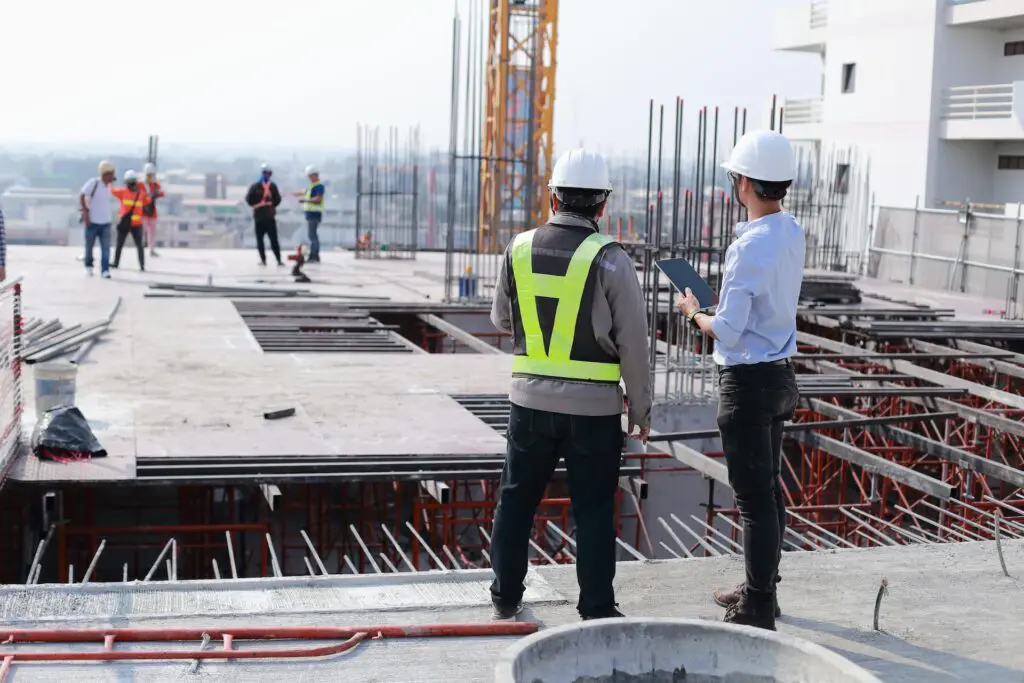
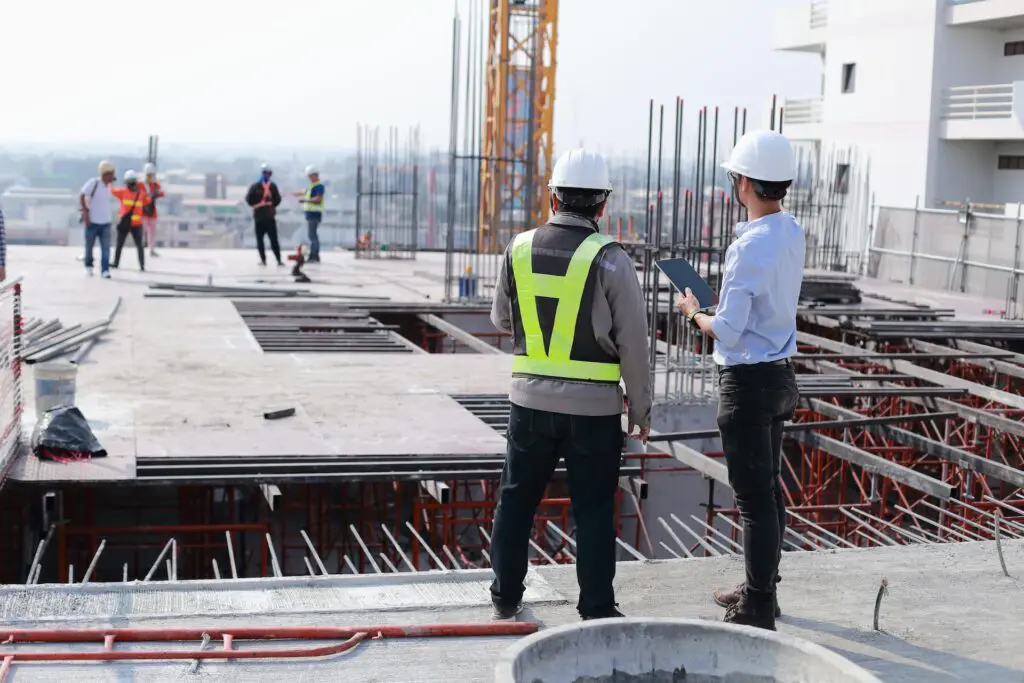

Want to share this article?
Debottlenecking: What It Is and How It Can Help Optimize Downstream Processes
At a glance
Part 1 of 2 on debottlenecking for downstream oil and gas—learn the basics of debottlenecking for refinery operations.
- Debottlenecking: What it is and why it’s important
- Strategic approach to debottlenecking: Evaluate and upgrade-retrofit-replace
- Safety and reliability: Why debottlenecking is critical for today’s aging refineries
- Benefits of debottlenecking: Increase throughput and ROI with advanced engineering
For more on the importance of debottlenecking in downstream oil and gas, read Part 2 of the series.
What is debottlenecking?
Debottlenecking in downstream oil and gas operations is the process of identifying specific areas and equipment in energy facilities that limit the flow of products—called bottlenecks—and optimizing them to increase overall capacity for refining and production.
Increasing the productivity of existing oil and gas infrastructure is critical for maximizing return on investment (ROI)—especially in times of economic volatility. High-value optimization and debottlenecking services restore competitiveness and empower operators to fulfill market requirements for efficient, accessible energy.
Most oil and gas plants, assets, and workflows have some degree of bottleneck inefficiency, from over-designed, over-engineered processes and reliance on sluggish supply chains to suboptimal technologies that increase the time and resources necessary for delivering quality end products. Taking a holistic approach is crucial for tackling bottlenecks and accelerating time to market while decreasing CAPEX/OPEX spend and meeting health, safety, and environmental (HSE) requirements.
Strategic approaches to downstream oil and gas debottlenecking and optimization
The first step in downstream debottlenecking involves examining the overall operating conditions of a facility. In many instances, this means comparing current operating parameters and system settings (flow rates, pipe diameters, pressures, etc.) with the design specifications of process equipment.
Eliminating a bottleneck can be as simple as changing system parameters to match recommended design values. Or the debottlenecking solution may require a bit more time and effort, such as replacing equipment or retrofitting it to better match the needs of the refinery.
Understanding the limitations of a facility is also a critical step in the debottlenecking process. While increasing throughput to some degree can be accomplished in nearly every refining process, it should never be done at the expense of safety.
Improvements for refinery safety and reliability
Debottlenecking is a proven solution for enhancing the safety and dependability of downstream oil and gas operations without requiring massive overhauls of existing assets. Most refineries in the US are over 50 years old, with many landing over the age of 100. Add to that the steady drop in the number of operating refineries, and plant operators are now facing major challenges to safely deliver high-quality product at high-volume demands while meeting updated regulatory requirements with older infrastructure.
Investing in debottlenecking is a cost-efficient way to boost the HSE profiles of downstream oil and gas operations, regardless of age or complexity. Injecting modern safety management, QA/QC, and risk mitigation techniques into in-place refining operations can help meet the latest regulatory requirements for continuous compliance. Additionally, cutting-edge capabilities can improve agility and minimize nonproductive time, which is key to reliable, efficient throughput.
Benefits of debottlenecking with integrated engineering solutions
Partnering with an experienced engineering company is a great first step in removing bottlenecks from downstream operations and achieving greater sustainability. Engineering services are often marketed as comprehensive or integrated, meaning they can address more than one type of debottleneck. It also often means that the debottlenecking solutions will work with or be tied into your existing equipment and processes.
Specific engineering services for debottlenecking include process analysis, feasibility study, detailed engineering and design, turnaround management, and in-plant engineering. Services like these delivered by a reputable engineering firm with oil and gas experience will eliminate bottlenecks and maximize productivity. They can also return a nonproducing plant to operations. What benefits can your downstream operations—and your ROI—experience without bottlenecks?
For more on the importance of debottlenecking in downstream oil and gas, read Part 2 of the series.
About the author
Shawn Senf is Vice President of Operations for Petrochemicals and Refining at Audubon Engineering Company. Shawn has more than 25 years of engineering and construction experience in the petrochemical and refining industry. His professional expertise includes EPC and EPCM projects for plants and facilities across industries. Shawn earned his Bachelor of Science degree in Mechanical Engineering from the University of Houston.
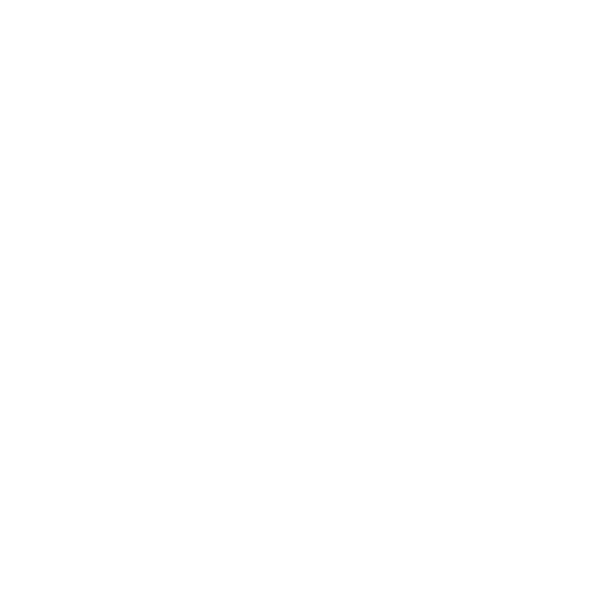