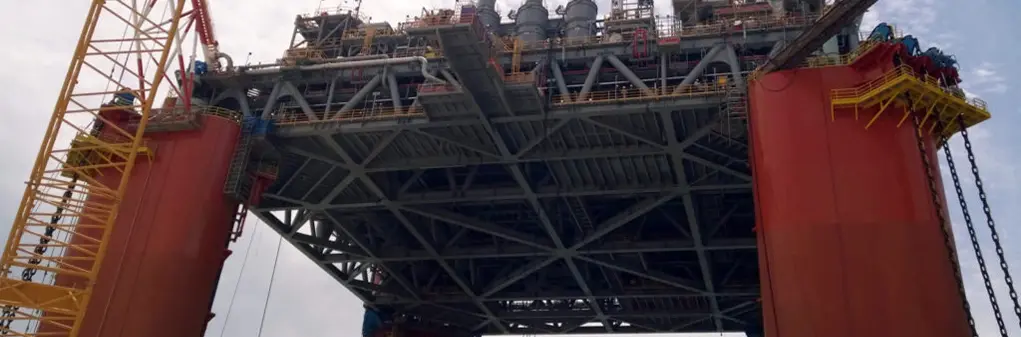
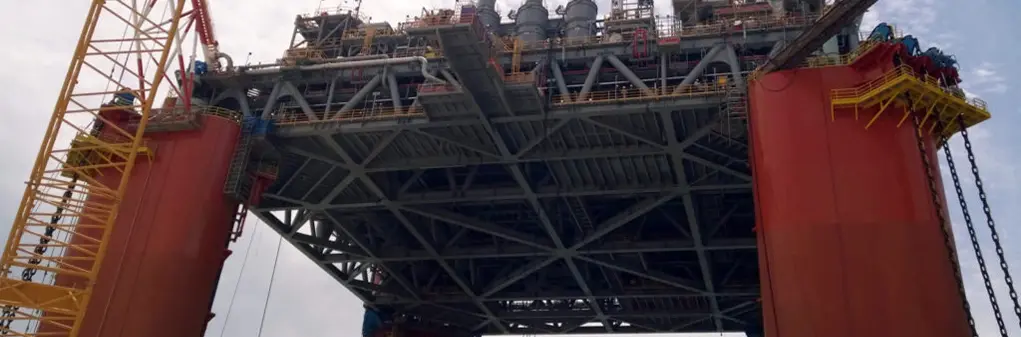

Want to share this article?
Technology Behind Subsea Production Systems
Completions of subsea oil and gas wells have been ongoing for more than five decades now, providing energy and manufacturing materials to the world.
However, the offshore exploration and development of these wells has become more challenging — and costly — as it has moved to deeper, more treacherous waters. This has forced companies to adopt more specialized subsea technologies to increase the productivity and longevity of their subsea completions.
An example of this kind of technology is found in a FMC Technologies-Statoil co-developed project that yielded the through-tubing rotary drilling (TTRD) intervention system. This has allowed producers to sidetrack into nearby hydrocarbon reserves more efficiently, increasing the longevity of existing wells. Production and quality control systems are another tool in producers’ belts. A collection of sensors tied to a software system can provide valuable data to allow for the optimization of production flow and the early detection of system problems to better mitigate unplanned maintenance and intervention.
Another modern technology employed by developers and producers is simulation and modeling software. Unable to apply a full-scale test in the real world, companies have turned to software simulators that can virtually test a proposed subsea production system to not only ensure it meets rigorous environmental and safety requirements but also detect expensive design errors that may result in project failure. Additionally, a variety of efficiencies and component behaviors can be measured to ensure the safest, most productive subsea design can be realized.
In addition to these technologies, other developments are in the works for deep and ultra-deep subsea completions. For example, specialized power cables and compression systems are being developed to help bring the entire production environment to the seafloor. Doing so provides theoretical advantages, according to GE’s Francesco Falco, including significantly lower maintenance and longer, more productive recovery rates.
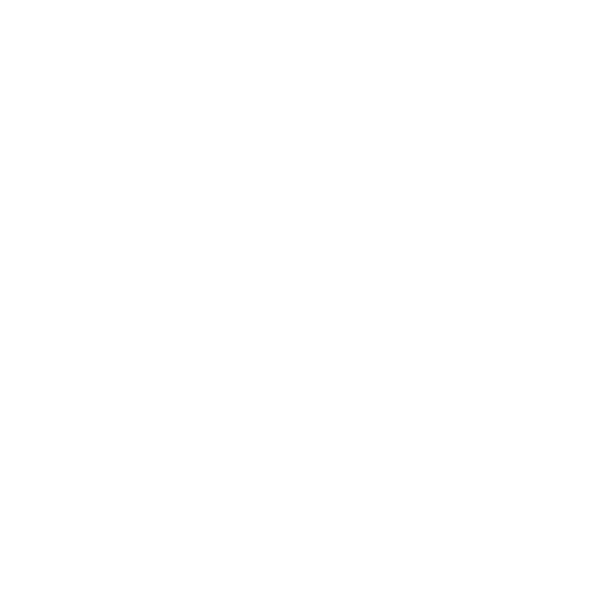