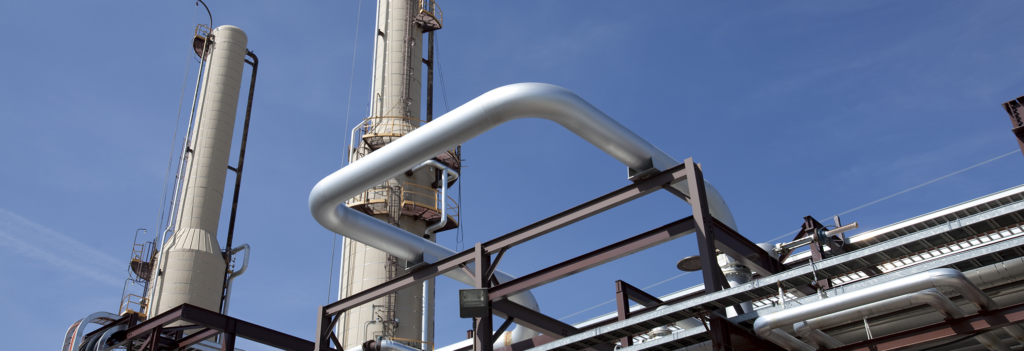
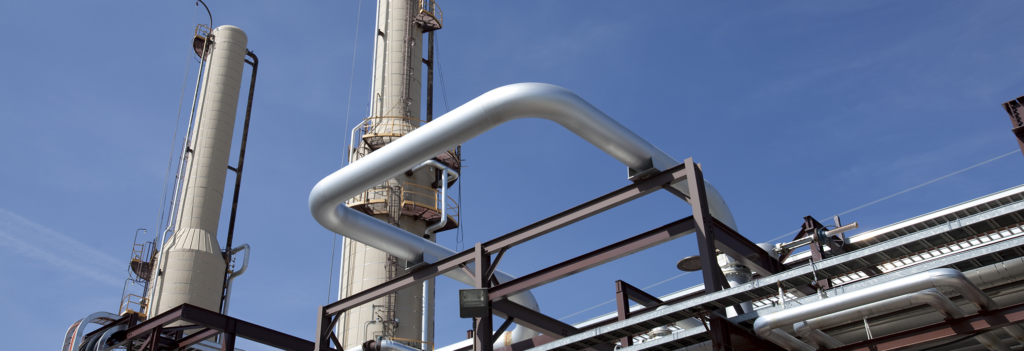
Natural Gas Processing Plant Outage + Upgrade on a Fast-Track Schedule
0+
man-hours with zero
safety incidents
0-Day
on-time
completion
0x
gas-processing
capacity
0+
ahead-of-schedule
activities
Operating thousands of miles of pipeline across the United States, a leading infrastructure company contacted Audubon to modify its natural gas processing plant in Texas. This plant processes offshore natural gas from the Gulf of Mexico.
Challenge: Strict 25-day outage needed for natural gas processing plant to prevent additional downtime & cost
The natural gas processing plant required substantial modifications to accommodate a new offshore gas stream. The modifications called for a planned outage to integrate piping tie-ins and to replace structures and equipment. For the incoming pipeline, shutdown time was limited to 25 days—meaning the processing plant needed
thorough planning and seamless execution for the outage.
The new gas stream, which more than doubles the plant’s original processing capacity, comprises hydrocarbons to be blended with existing onshore product. To meet the new capacity, the processing plant upgrades also included a new product stabilizer, compression equipment, pressure vessels, and meter skids, as well as modifications to existing cryogenic facilities.
Solution: Technical expertise showcased in robust EPFC solutions
Outage planning & equipment replacement
To accomplish the plant outage and upgrade within the 25-day timeline, the plant operator enlisted Audubon for comprehensive, integrated engineering, procurement, fabrication, and construction (EPFC) services. Audubon collaborated with the client’s team to plan the outage, design the facility modifications, and replace equipment:
- Pressure vessel
- Molecular sieve beds (internals)
- Demethanizer tower (internals)
- Pumps
- Turbo expander (center sections)
- Tie-ins
During the outage, the construction team demolished the existing pressure vessel and installed a larger one including the piping, piles, supports, and instrumentation and electrical (I&E) system. Automation personnel implemented and calibrated new controls for the upgraded cryogenic facility for precise, reliable operation. Upon startup, the cryogenic unit had no equipment leak.
Additionally, three pumps were removed, optimized, and reinstalled according to new processing specifications. Modifications were made to molecular sieve beds, piping, and valves to allow for cryogenic bypass and gas blend. To upgrade the turbo expander for the new conditions, the team designed and replaced its center section. Audubon also inspected the demethanizer tower to plan replacement of its internal system.
Two-product stabilizer design & fabrication
Outside of Audubon’s scope during the outage, Opero Energy designed and fabricated a new two-product stabilizer unit and associated modules for the plant. Applying processing expertise, Opero Energy utilized a modular design approach to ensure a turnkey solution for the new and upgraded equipment.
Results: Processing plant put back online with improved efficiency & productivity
The natural gas processing plant outage was successfully executed within the allotted 25-day timeline, with many modifications completed ahead of schedule. Audubon applied critical project management capabilities to coordinate activities among all personnel, logging zero safety incidents over 30,000+ man-hours, including
hundreds of personnel across more than a dozen subcontractors.
For the outage portion of the plant upgrade, Audubon’s team collaborated with stakeholders to execute a suite of EPFC services. Engineers, project managers, welders, pipe fitters, I&E technicians, fabricators, and others worked together to make the plant outage a success. After completion of the full plant upgrade, the company will be
able to expedite processing and blending operations for more natural gas arriving from the Gulf of Mexico.
Scope of work
- Engineering & design
- Procurement
- Fabrication
- Construction
- Inspection
- Automation & control
- Project management
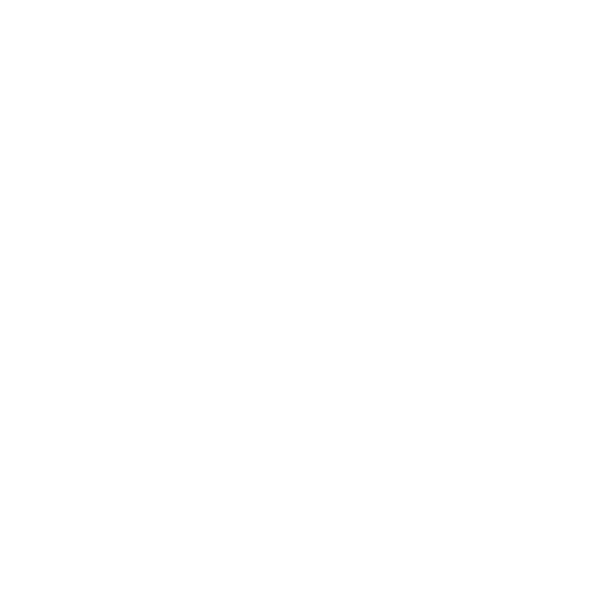