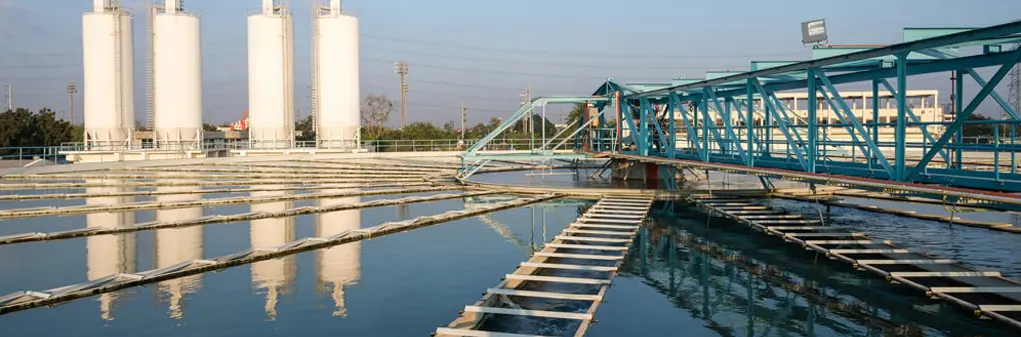
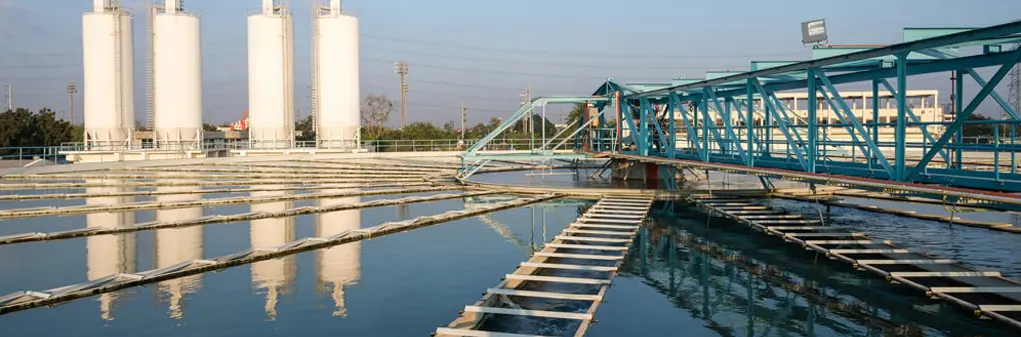

Want to share this article?
Potable Reuse of Produced Water: Part 2
In the first part of our discussion on reusing produced water, we briefly looked at the numbers and considered the factors that play into an extraction company’s associated water management plan.
We stated water properties, budgets, available technology, research, and public opinion all affect decisions on the potable reuse of produced water. Let’s take a closer look.
As Matthew E. Mantell, an environmental engineer for Chesapeake Energy, put it for an EPA hydraulic fracturing workshop in 2011 (PDF), “feasibility of produced water reuse is [in part] dependent on three factors: quantity, duration, and quality of produced water generated.” Regarding the first two factors, whether using conventional or unconventional production methods, many wells generate produced water at varying amounts for varying durations over the lifetime of the well (PDF). Conventional wells often produce little produced water initially but increase gradually over the lifetime of the well, leading to a large overall quantity. However, unconventional production methods, particularly from shale and coal seams, are capable of generating significant quantities of produced water in the first 10 days of production but rapidly tail off for a low lifetime quantity. As for the final factor, quality characteristics of produced water also matter, including hydrocarbon, metal, calcium, magnesium, and salt content. For example, water with salinity that can’t be lowered (through blending or filtering) to less than 1,500 ppm TDS (total dissolved salts) is virtually unusable for irrigation. Even the presence of bacteria may dictate treatment and usage options.
Additionally, Mantell noted a direct correlation between environmental benefits and the economics of reuse vs. disposal. As the Society of Petroleum Engineers (SPE) notes, treatment costs are largely based upon the previously mentioned variables. “Therefore, technology solutions for potable reuse of produced water would need to be customized accordingly to the properties of the produced water and the amount of water to be treated.” These costs can be high with associated treatment technologies such as oxidation and ceramic membrane filtration.
This has prompted producers as well as commercial companies to fill in existing research gaps and investigate new and novel ways to more efficiently and cost-effectively treat produced water for potable reuse. In addition to creating their own novel treatment solutions, companies such as GE and Statoil have also begun offering cash awards and research funding for top research teams able to provide viable solutions for improving produced water use and treatment for onshore oil and gas production.
Finally, as the SPE notes, the general public’s perceptions of produced water reuse also pose a challenge. “Although existing technologies have been demonstrated to meet current drinking water standards,” the group says, “there are concerns on unknown toxic effects or unknown toxic compounds … in the treated produced water.” Researchers such as Theodori et al. propose the implementation of public outreach programs (PDF) using a variety of delivery methods that aim to educate the populous on what desalination and other filtration technologies are or are not capable of doing.
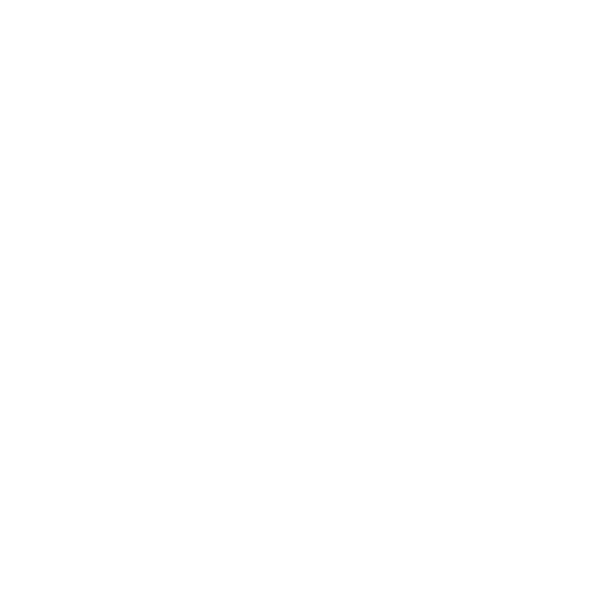