


Want to share this article?
Managing Stress Corrosion Cracking (SCC) with Pipeline Integrity Management Techniques
Stress corrosion cracking (SCC) in oil and gas pipelines can be extremely problematic.
It occurs when a combination of internal stress from high pressure contents inside a pipe and corrosive agents outside the pipe cause the formation of interlinking crack clusters.
Despite very small amounts of metal loss, the formation of these clusters effectively reduces pipeline strength, which in turn can lead to any number of costly issues including repairs, replacements, leaks, spills, breaks, and in some severe cases, total pipeline failure.
Pipeline integrity management techniques have proved to be the most effective method of mitigating SCC and preventing these costly failures from occurring. The most prominent of these techniques include:
Direct assessments involve collecting existing information on the pipeline that can be used to determine the likelihood of stress corrosion cracking from occurring. This includes temperature of the product, operating stress, age of the pipeline, coating type, and distance to the compressor station. Thoroughly examining the environmental conditions of the location that a pipeline is in also helps determine if SCC will be a problem.
In-line inspection pigging is also widely used to assess pipeline integrity. During this process, mechanical vehicles known as pigs are inserted into a pipeline where they can gather valuable information relevant to pipeline integrity, including pipe diameter, temperature, and pressure. This is done either through magnetic flux leakage or ultrasonic (or both) and helps identify any leakage points or weaknesses in the pipeline.
Lastly, hydrostatic testing involves filling a pipeline with water and then pressurizing it to a level that exceeds normal operating conditions. Generally, the pressure is held at this level for many hours and it is a highly efficient method of identifying areas of extreme weakness in pipelines.
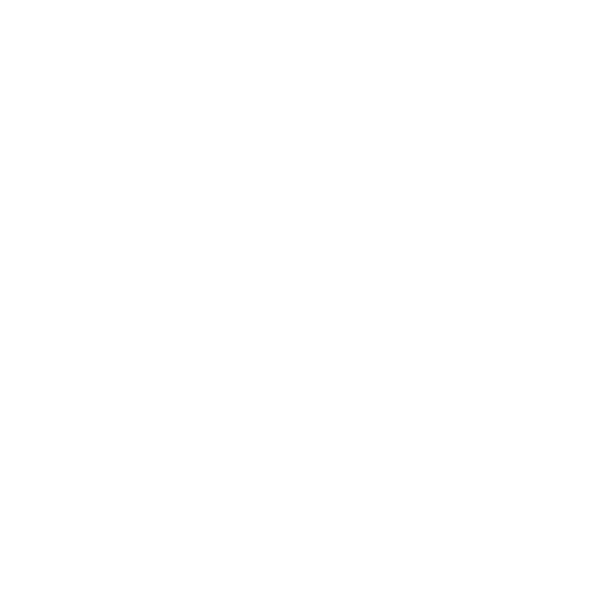