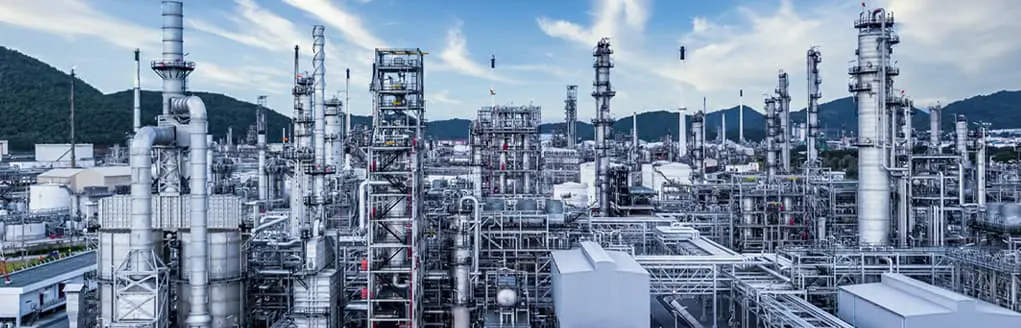
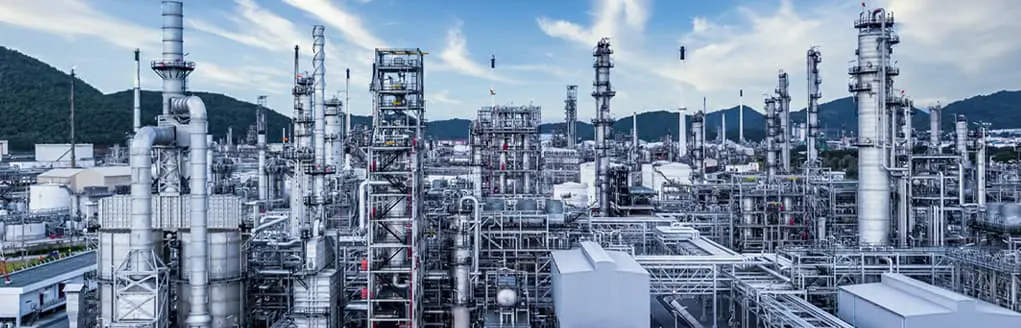

Want to share this article?
Importance of Debottlenecking in Downstream Operations
At a glance
Part 2 of 2 on debottlenecking for downstream oil and gas—discover the importance of debottlenecking for refinery operations.
- Economic benefits: Effective debottlenecking decreases life-of-asset costs
- ROI improvements: Debottlenecking improves returns on aging infrastructure
- Engineering’s role: Considering the whole plant
- Debottlenecking success: Proven experience for project execution
For more on what debottlenecking is in downstream oil and gas, read Part I of the series.
Economic benefits of debottlenecking in downstream oil and gas
Debottlenecking can increase production capacity, reduce downtime, improve efficiency, and enhance sustainability for downstream oil and gas operations—all leading to increased profitability.
One of the most significant benefits of debottlenecking is increased throughput. By removing bottlenecks, operators can increase production capacity—without the need for major capital investment or whole-facility expansion. With increased capacity, operators can take advantage of market opportunities, fulfill orders more quickly, and generate more revenue.
By improving operational efficiency, debottlenecking can minimize the time required for maintenance and repairs, thus reducing downtime and increasing uptime.
How debottlenecking improves ROI in refinery operations
Most refineries in the US are over 50 years old. After decades of operation, facilities may no longer be running at peak efficiency. Furthermore, many refineries have closed in recent years—so maximizing the value of existing refineries is more important than ever to the E&P sector.
Knowing what facets are curtailing productivity is the first step to remediation. Debottlenecking studies can reveal opportunities to improve efficiency and performance in existing legacy infrastructure with minimal investment. For example, a downstream refinery might be offloading a feed-gas supply that could be monetized, or a control system might be throttling equipment performance without the operator knowing it.
These types of efficiency limiters can be unearthed with a debottlenecking study. Compared with an extensive overhaul of in-place infrastructure and ways of working, a debottlenecking project will improve returns from existing investments.
Achieving quality and safety by debottlenecking plant processes
The primary goals at any facility are safety and quality. An effective debottlenecking process improves product quality and reduces health, safety, and environmental (HSE) risk. By optimizing processes and equipment, debottlenecking can ensure that products meet quality standards and comply with regulatory requirements, resulting in fewer quality issues and regulatory violations. Without fines or penalties, an operator further saves cost and protects the company’s reputation.
After studying current processes and operations at a refinery, a knowledgeable debottlenecking team will recommend modern techniques for safety management, QA/QC, and risk mitigation. These improvements translate to both human safety and reliable operations.
Engineering’s critical role in debottlenecking downstream operations
Identifying the source of a problem and implementing an optimal solution requires extensive engineering expertise. The right approach should consider the facility’s past, present, and future to ensure long-term success. In many cases, the problems can be remedied by marginally changing the production process or enacting minor modifications in plant and equipment. Other times, facility turnaround is required. Whether simple or complicated—a debottlenecking process mandates specialized engineering acumen.
In the past, debottlenecking studies have largely looked at operational problems as something that can be isolated and resolved. However, the advent of modeling and simulation software, as well as new, broader approaches to debottlenecking have expanded it to consider the entirety of plant operations instead of piecemeal solutions.
Modern digital capabilities, including automation, machine learning, and artificial intelligence, can also effectively enhance productivity of staff and technology to more quickly deliver high-quality product to end users.
How to achieve debottlenecking project success
When deciding which refinery projects to prioritize and which service providers to hire for them, it is important to consider not only cost and timeline, but also the expected result from the project investment.
An engineering company with proven experience specifically in the oil and gas industry will bring precise knowledge and the right solution to your project. For the best outcome, look for comprehensive engineering services beginning with conceptual study and front-end engineering and design (FEED) so that fit-for-purpose upgrades are made for your particular operations. Safety and process risk analyses are also important elements of a successful debottlenecking project, which should always be prioritized by a reputable engineering services company.
Getting expert engineering support for debottlenecking will result in better project execution for maximum throughput. How can successful debottlenecking improve your production and reduce your risk?
For more on what debottlenecking is in downstream oil and gas, read Part I of the series.
About the author
Shawn Senf is Vice President of Operations for Petrochemicals and Refining at Audubon Engineering Company. Shawn has more than 25 years of engineering and construction experience in the petrochemical and refining industry. His professional expertise includes EPC and EPCM projects for plants and facilities across industries. Shawn earned his Bachelor of Science degree in Mechanical Engineering from the University of Houston.
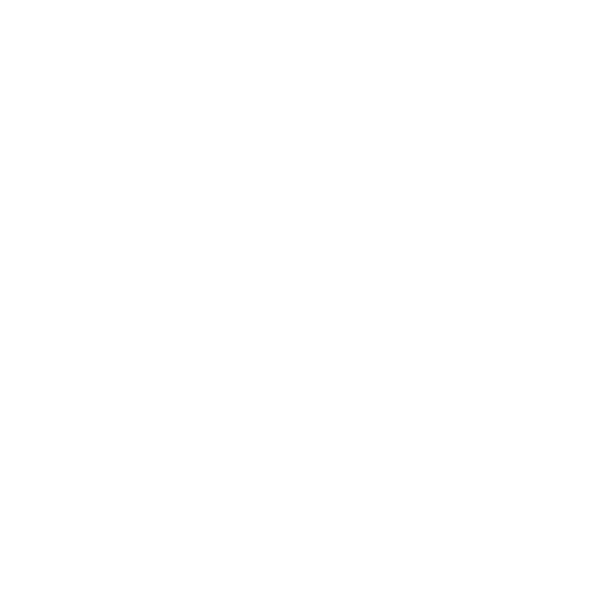