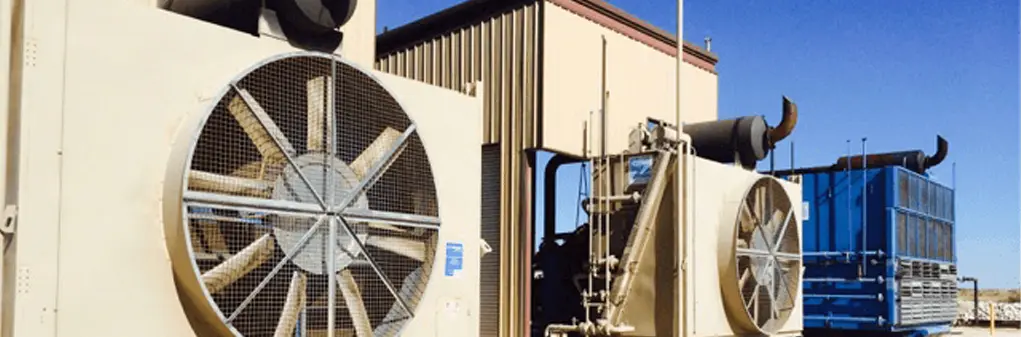
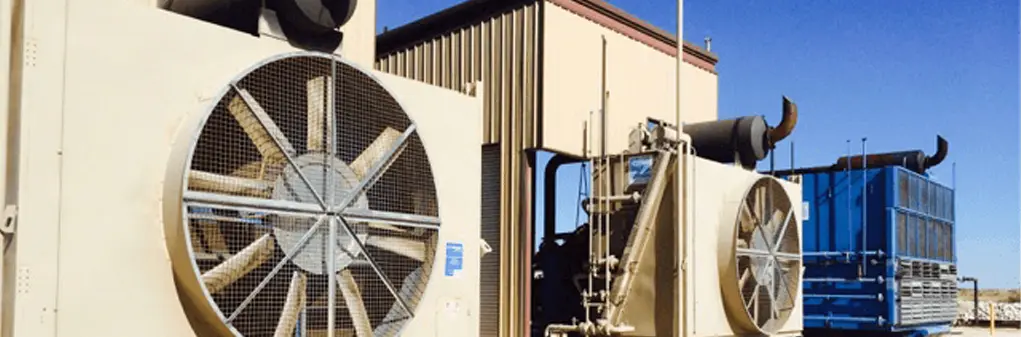

Want to share this article?
Components of a Compressor Station
Compressor stations are a vital part of any gas transmission system, keeping gas at a particular pressure so it can continue to flow to its destination.
According to numbers from the U.S. Department of Transportation Pipeline and Hazardous Materials Safety Administration, the U.S. had 1,768 compressor stations in operation along its pipelines in 2013. Most appear along the interstate pipeline system at intervals of 40 to 100 miles. Of installed compressor types at those stations, 91.6 percent were reciprocating compressors, with centrifugal compressors making up the other 8.4 percent. The type of compressor used is determined by a number of factors, including efficiency, flow rate, and load control.
Reciprocating compressors — which have been around since the first half of the twentieth century — work off the concept of positive displacement, using pistons in reciprocating motion to compress and displace gas. Most are powered by natural gas and are useful for low-volume flow conditions. They excel in situations where capacity, gas composition, and pressure vary.
Centrifugal compressors are a more recent addition, relying on the use of a continuous flow of gas through an impeller. The speedy flow is then decelerated in a diffuser and volute, which subsequently causes the flow’s pressure to rise. Most are powered by electricity and are useful for high-volume flow rates. They excel in situations where capacity, gas composition, and pressure are relatively constant.
While the compressors themselves are the key components, a compressor station has other important facets as well. Incoming feed gas must be filtered to remove solids and liquids that may have accumulated or condensed out during transport from the previous compressor station or source. Outgoing gas, having run through the compressors, must also be cooled before returning to the pipeline since the process of compression raises the temperature, which can damage the inner protective coating. Emergency shutdown systems are also vital, shutting down engines and isolating and venting gasses during abnormal conditions. Noise is also a concern, with special regulations that state that noise levels can’t exceed 55 decibels to the closest residence or within 300 feet when on state forest land. This means mufflers are put in place on exhaust and intake systems. It also means in many cases sound-reducing infrastructure and insulation is built to enclose stations and reduce sound levels.
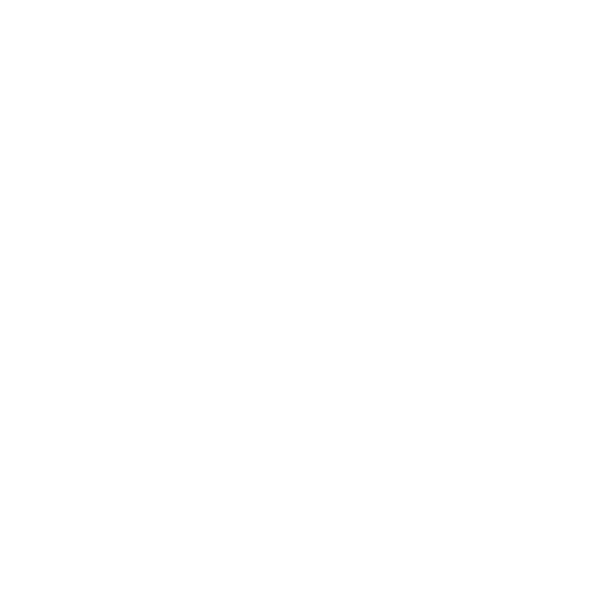