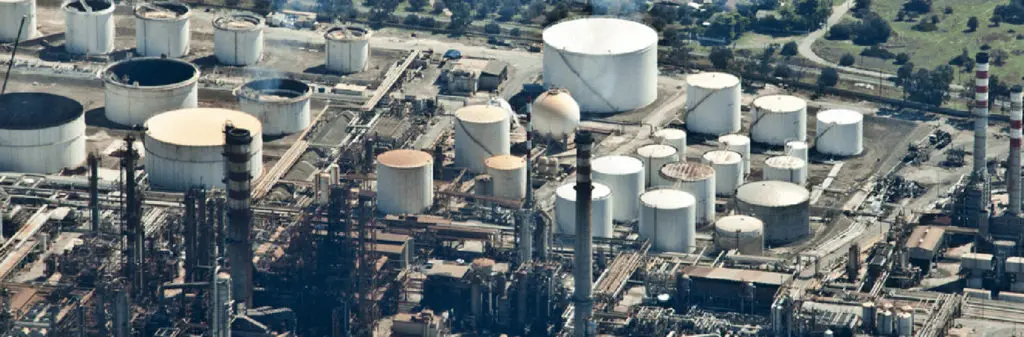
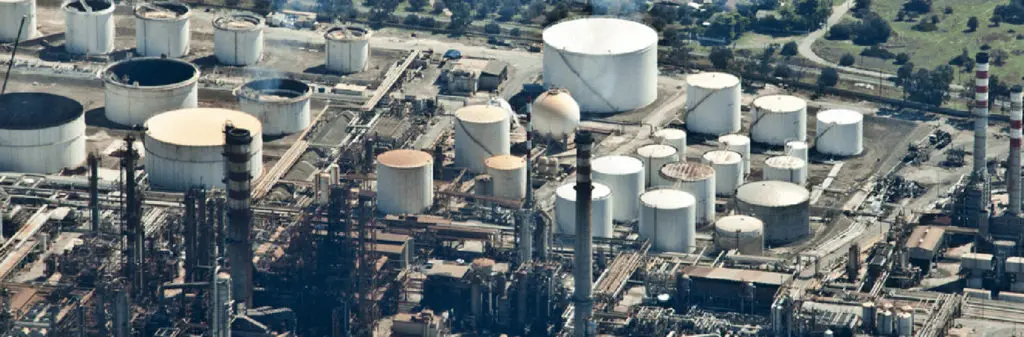

Want to share this article?
A Broad Look at Hydrocarbon Measurement
Production facilities receive hydrocarbons from the wellhead via pipelines or some other transportation method, and likewise, the finished products and waste leave the facility in a similar manner.
All along the chain are custody transfers, safety analyses, and production reports, each requiring accurate flow, level, pressure, and temperature measurements.
Hydrocarbon measurement (PDF) occurs at many stages and for many reasons, from well testing and wellhead flow to processing and transportation. During the field processing phase, for example, oil and gas is treated to specific standards for sale and distribution. This includes separating water, dissolved gases, and other impurities from oil and removing liquids and acid gases from natural gas. In many cases those removed liquids and gases must then be managed for reinjection or disposal. In order to maximize uptime and profits while minimizing risks to workers and infrastructure, a consistent and accurate automated measurement process is required.
The type of hydrocarbon measuring equipment (PDF) employed will vary based on the process, product characteristics, desired output, and level of accuracy required. Product with high viscosity and heavy contamination requiring a high level of measurement accuracy may require a different device than a product with low viscosity and contamination requiring a lower level of accuracy. Flow meters such as positive displacement, turbine, and electromagnetic flow meters are the typical measurement device for custody transfers and efficiency monitoring.
Aside from flow measurements, level detection is another important type of measurement used in hydrocarbon production. They can be applied in relatively simple circumstances like final tank storage or more challenging situations, including in multi-fluid vessels such as high-pressure separators. Magnetic level gauges, guided wave radar level transmitters, and ultrasonic level transmitters are common examples applied across a wide variety of situations. Pressure, temperature, pH, turbidity, and conductivity represent other properties that must be measured effectively. In all cases, proper calibration and maintenance are essential towards extending measurement device lifetimes, improving safety, and maintaining overall profitability.
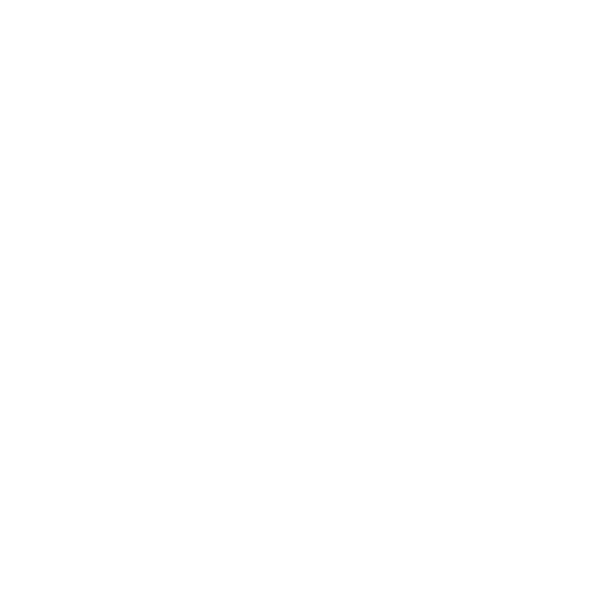