PAUL HEBERT
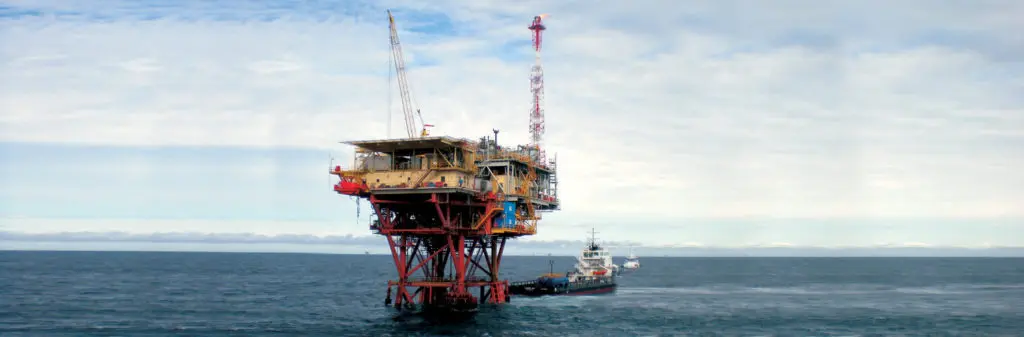
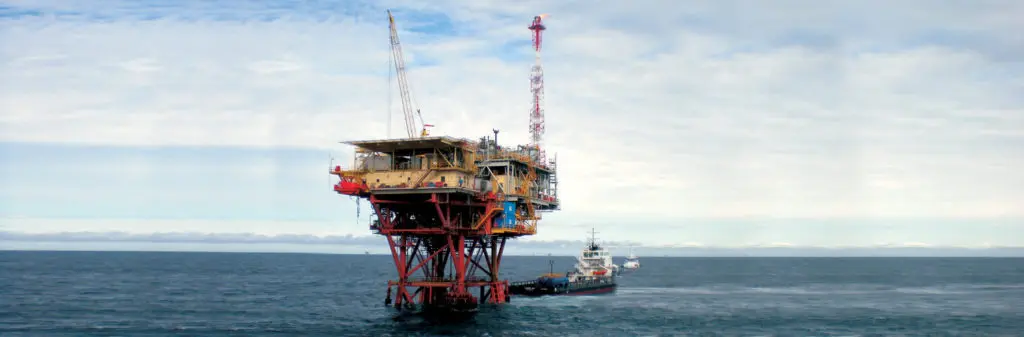

Want to share this article?
How Early Planning Can Improve Offshore Decommissioning
Decommissioning is a necessary part of offshore oil and gas production – one that many operators start preparing for in the later stages of a facility’s lifecycle.
However, for as difficult and resource-intensive as the decommissioning process can be when it comes to complex offshore structures, companies can benefit by planning early and adopting a strategic approach.
Although decommissioning of land-based infrastructure presents fewer challenges with regards to safety, engineering, and cost when compared to offshore assets, there are many onshore methodologies that operators can apply to improve their deepwater decommissioning efforts.
One such practice is to increase the frequency of audits and inventory checks throughout the life of a platform and/or floating facility. Because they are in service for decades, these structures often undergo multiple changes and modifications in order to meet the constantly evolving requirements of the reservoir. This includes topsides equipment changes, piping repairs, instrumentation replacements, and system additions. Having a database that keeps track of such changes and accurately reflects the current state of the facility will help to determine the proper course of action for every piece of equipment after the facility is shutdown (recycled, scrapped, sold, etc). Not performing audits frequently and thoroughly will more times than not result in unexpected difficulty during the decommissioning process – opening the door to potential delays, added complexity, and most importantly, higher costs.
Structural integrity also plays an important role when it comes to offshore decommissioning. For instance, a damaged and/or corroded section of a platform or drilling rig may make it unsafe for personnel to decommission a single piece of equipment. Even though the piece of equipment might play a very small role in the overall decommissioning effort, accessing it could require repairs or even the installation of scaffolding. If this wasn’t a contingency that was addressed in the original decommissioning plan, it can lead to even further delays, more risk, and additional manpower requirements.
Performing routine inspections, particularly in the years leading up to facility shutdown, is key to avoiding surprises that can derail a decommissioning plan. Doing so also provides the added benefit of being able to identify issues with equipment and schedule proactive maintenance to keep it in proper working order.
Above all, operators must approach offshore decommissioning efforts strategically – planning early and planning often from the day the facility goes into operation, all the way through to when the last piece of equipment is transported offsite to its final location.
Offshore Division Vice President
Paul Hebert is the Offshore Division Vice President at Audubon Field Solutions. He has over 40 years of experience in construction management and domestic and international business development in the onshore and offshore oil and gas markets. In his current role, Paul manages Audubon Field Solutions’ offshore field operations.
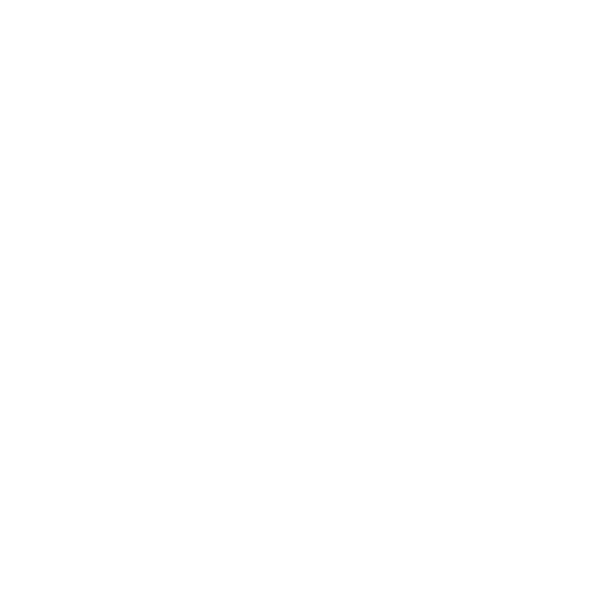