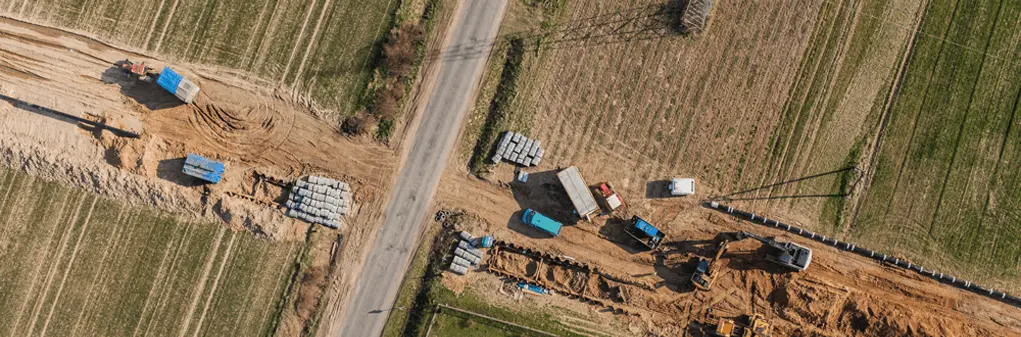
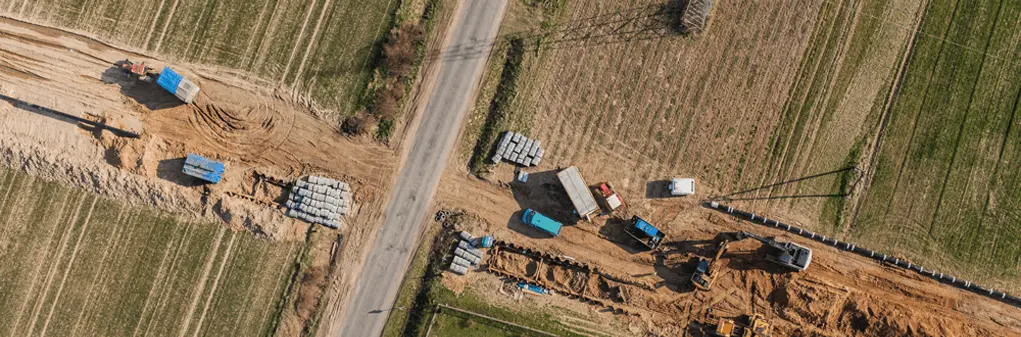

Want to share this article?
Pipeline Integrity Makes All the Difference
This blog post is the first of our five-part blog series about Pipeline Integrity Management.
For nearly 50 years, natural gas pipeline networks have been the preferred method for transporting materials, such as crude and gas, due to cost-effectiveness and overall efficiency.
With approximately 300,000 miles stretching across the U.S., pipelines transport and distribute 100% of natural gas and approximately 67% of oil. These pipeline systems are also considered the safest transportation option for fuel and other hazardous materials. When compared to pipelines, accidents involving large trucks are 1,000 times more likely to occur, 13 times more likely to occur by barge, and 5 times more likely to occur by rail. Still, a myriad of factors can cause pipelines to develop defects and ultimately fail. Compounding these risks is the fact that many of today’s existing pipelines were laid in the 1970s without the benefit of current pipeline regulations and standards. As they continue to age, these pipelines become even more susceptible to external and internal damage like corrosion. Without proper design, construction, and maintenance, the lifecycle of pipelines becomes shortened, subsequently exposing people, animals, and the environment to dire consequences. This is where pipeline integrity management comes into play.
Pipeline systems are considered the safest transportation option for fuel and other hazardous materials. To help safeguard against pipeline failure, operators and owners engage in preventative safety measures known as pipeline integrity management. Whether greenfield or brownfield, pipeline projects must have a consistent, comprehensive Pipeline Integrity Management Plan or Program (IMP) in place to ensure the safety and reliability of a pipeline, especially for pipelines that run through or near high consequence areas (HCAs). Major causes of failure in both offshore and onshore pipelines include outside forces (e.g., third-party or mechanical damage) and internal/external corrosion (i.e., caused by the product being transported or the environment). Construction/material defects, equipment/operator error, and other scenarios may also cause a pipeline to fail. The most common type of failure for transmission pipelines is internal pressure loading on a part wall defect or pipe damage.
Developing an effective IMP can be complex. This systematic monitoring and maintenance program requires the expertise and integration of several technical disciplines (e.g., engineering, risk management, geographic information systems, etc.). It also involves inspection, assessment, mitigation, and communication to address any potential threat to pipeline systems. Common key elements of IMPs include audit and baseline assessments, inspection and maintenance, training, engineering and design, risk and reliability, fitness for service, operation control and monitoring, and repair and rehabilitation. All IMPs should follow guidelines established by the U.S. Department of Transportation (US DOT), governmental agencies and local regulators in efforts to facilitate compliance. Formalizing IMPs at the governmental level was necessary because the oil and gas industry has experienced many significant pipeline failures, particularly those resulting in the loss of human life. One such incident involved a major pipeline that leaked from 1990 to 1997 in Texas, Oklahoma, Kansas, Alabama, Louisiana and Missouri. The cited cause was the lack of pipeline maintenance. The company responsible was issued “the biggest civil fine levied under the Clean Water Act,” according to the Environmental Protection Agency (EPA). Other incidents include an onshore gasoline line failed in 1999, causing product to leak into a nearby river and spark an explosion that killed three young people. In 2000, 12 campers were killed when an onshore gas line failed.
To counteract the number of incidents occurring as well as growing public scrutiny, the industry sought to put in place regulations and guidelines that would standardize pipeline integrity on a federal and state level. In 2004, the US DOT created the Pipeline and Hazardous Materials Safety Administration (PHMSA) to monitor pipeline infrastructure across the country and to develop pipeline transportation regulations to govern integrity management processes. The goal of the these regulations was to accelerate the integrity assessment of pipelines in HCAs, enhance operator integrity management systems, improve the government’s role in reviewing the adequacy of integrity programs and plans, and provide increased public assurance in relation to pipeline safety. The regulations took effect in 2004. A continued, concerted effort by the industry is key to strengthening pipeline infrastructure in the years to come. Additionally, the American Petroleum Institute (API) issued an industry standard for developing pipeline IMPs, specifically for pipelines carrying liquids. For instance, operators now must develop and implement an IMP that identifies all pipeline segments that can potentially affect an HCA if failure occurs. The IMP must also have a timeline for performing a baseline assessment to evaluate the pipeline system’s condition, including internal inspections or hydrostatic tests. Likewise, the American Society of Mechanical Engineering (ASME) issued an appendix with similar guidance for its gas pipeline design code, ASME BE31.8. When combined and strictly adhered to, these standardized design criteria help to prevent failure caused by burst, puncture, overload, buckling, fatigue and fracture.
Legislating integrity management has proven to be effective, and the decline of pipeline incidents speaks to its success. Since the industry decided to collectively follow state, local and federal regulatory requirements, incidents caused by corrosion are down by 76%. Operational error is also down by 53%, equipment failures are down by 26%, and material and weld failures are down by 23%. Over the last 10 years, crude oil spills are down by 59%, and spill volumes are down by 43%. These numbers not only indicate the importance of pipeline integrity management, but that a continued, concerted effort by the industry is key to strengthening pipeline infrastructure in the years to come.
Stay tuned for our next blog post, “Pipeline Integrity Plus Risk Management Can Equal Zero Incidents,” where we discuss how pipeline integrity is an integral part of risk management and fostering a culture of safety within companies.
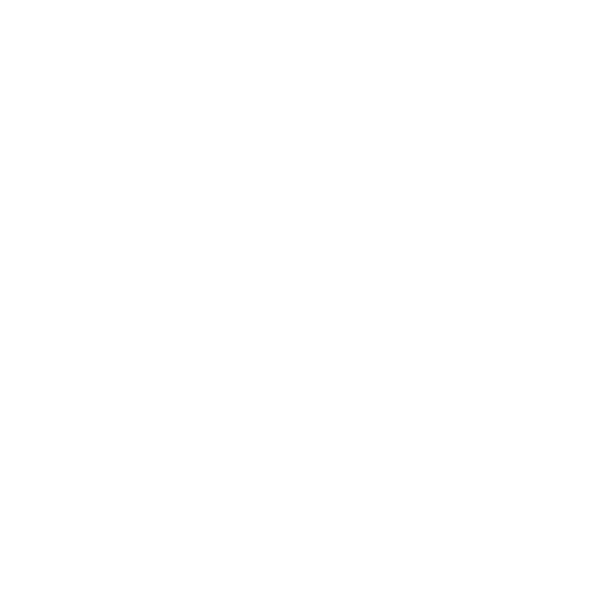