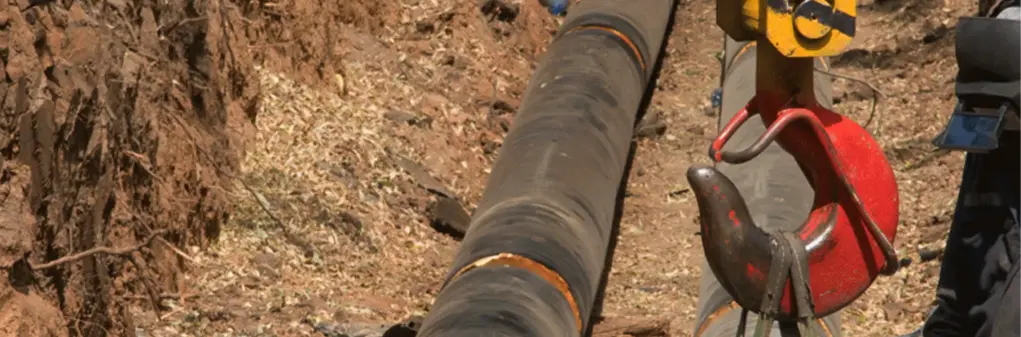
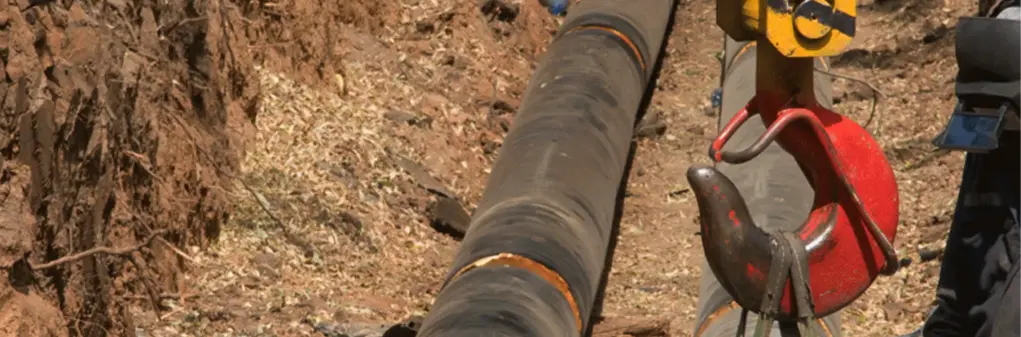

Want to share this article?
Developing and Implementing a Pipeline Integrity Management Plan
Over time, both onshore and offshore oil and gas pipelines degrade from corrosion and degradation caused by normal operation.
As such, regular auditing of existing pipeline infrastructure is required to ensure quality flow rates as well as conformance with increasingly rigorous safety and environmental regulations. Maintaining pipeline integrity is of vital concern to operators, and they do this best with a well-designed pipeline integrity management (PIM) plan.
Clues to what a PIM plan must achieve can be found in the U.S. Department of Transportation’s (DOT’s) hazardous pipeline integrity management rules codified under 49 CFR 195.452. As the DOT states, pipeline integrity management isn’t solely an inspection of pipe conditions; it also involves the development and implementation of “improved management and analysis processes” and additional risk-prevention measures. Developing such processes and measures is a comprehensive activity that requires understanding of codes and standards (like ASME’s B31.8S and API’s 1160), the required elements of an integrity plan (including threat identification and performance planning), prevention and mitigation methods (like maintaining coatings and surveying from the air), and the strengths and drawbacks of applicable inspection methods.
Pipeline integrity management plans must details how processes will be implemented, from beginning to end. They must also detail who will make applicable decisions concerning integrity checks and maintenance as well as how they’re made. Additionally, the various elements of the integrity management program must fall under a realistic schedule, including who will enact them and how. Finally, the plan must also take into account how the plan itself will be assessed and improved in the future based on previous experience and feedback. Data management tools like PIM systems and mineable databases assist in the assessment process, providing valuable data on the health of a pipeline network and any repairs and mitigation required over time.
Or course, when deficiencies are identified, they must be rectified. Qualified maintenance and repair personnel must be employed to conduct pipeline integrity change-outs and repairs. Pipeline mains may require full encirclement sleeve repairs or complete replacement of defective pipe, at times in difficult-to-manage locations like under roadways or railroad crossings. Other repair techniques include grinding out shallow defects, depositing weld metal, and mechanically bolting on clamps to contain leaks.
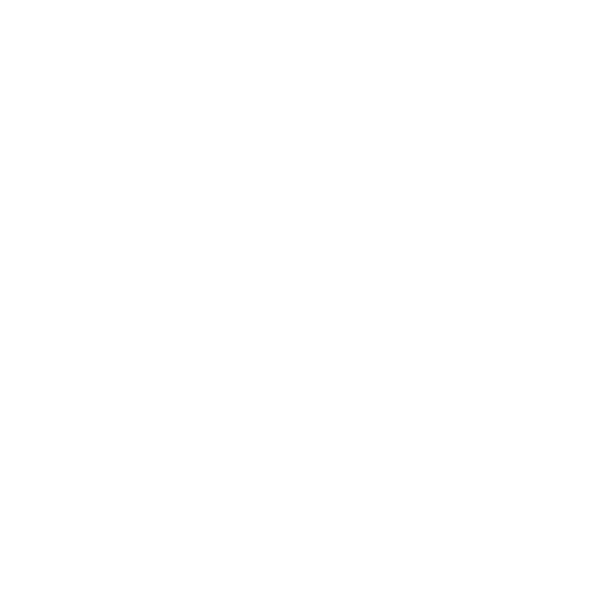