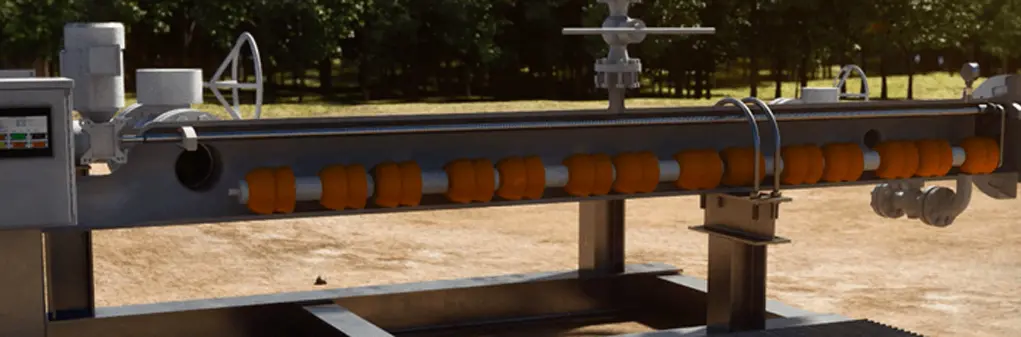
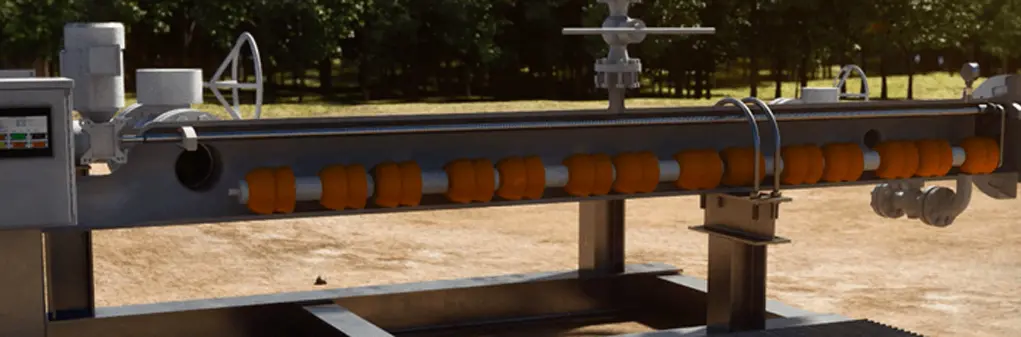

Want to share this article?
Pigging Systems Go Automated
In 1994, the U.S. Department of Transportation codified regulations that would require oil and gas pipeline operators to “accommodate the passage of instrumented internal inspection devices.”
Thus smart pigs were born to gauge the physical condition of pipelines. These pigging devices, however, have evolved since then into hundreds of types used not only for inspection but also other maintenance activities. These devices have traditionally been introduced into systems using several types of manual launching and receiving stations. However, as with many functions in oil and gas operations, pigging is becoming a more automated process.
Automated pigging systems are now being developed and implemented to handle primary functions like cleaning, separation, recovery, and inspection with less human interaction and fewer valve cycles. The pigs used to complete these functions vary based upon the necessary task. Cleaning applications are performed with numerous types of pigs, with magnets and scraping elements attached to some models. These pigs scrape, brush, and push foreign deposits, debris, and liquids from the pipeline. Mandrel or single-cast urethane pigs can be used to separate or batch a variety of different products transported through the same pipeline simultaneously. Batching pigs can reduce the interface between gasoline and another fuel oil, for example, so both can be ushered through the line at the same time. Polyurethane, foam, and spherical pigs can be used to recover residual product left behind from a process. And special mapping, crack-detection, and metal-loss inspection tools can be inserted to gauge a pipeline’s structural integrity.
While an automated pigging system and its pigs can handle the same functions as a manual system, what are the advantages of going automated? Simply put, manual systems are more labor- and maintenance-intensive. They require more valve use, draining, and venting. Valve systems can deteriorate more rapidly, and workers are placed in more situations that require safety vigilance. When implemented well, automated pigging systems reduce manual work hours (as well as exposure), cut down on valve cycles, and shrink maintenance costs. As such, field service companies like Audubon Field Solutions and WeldFit Energy Group are increasingly turning to automated pigging as part of their service offerings. Using their expertise in project management and the inherent benefits of the automated system, these companies can reduce operational and maintenance costs as well as improve the overall return on investment of a pipeline project.
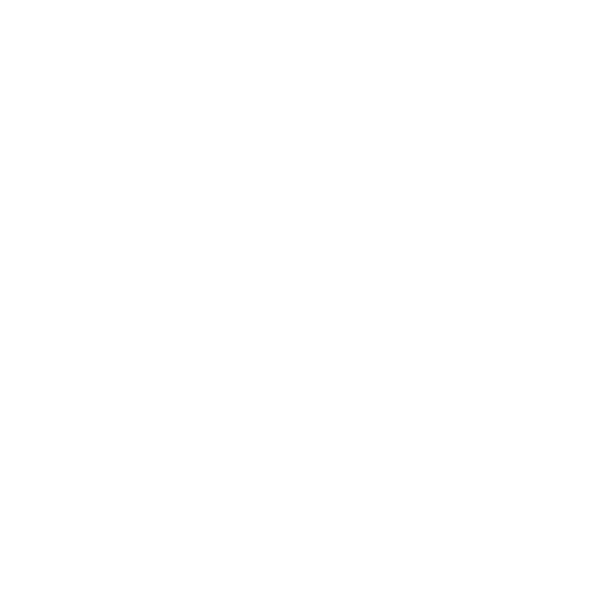